Flashings
Metal Roof Flashings
The following range of roof flashings have proven to be universally popular and suitable for most applications. Minor local variations may exist from that shown. Dimensions are nominal and may vary with changes in material.
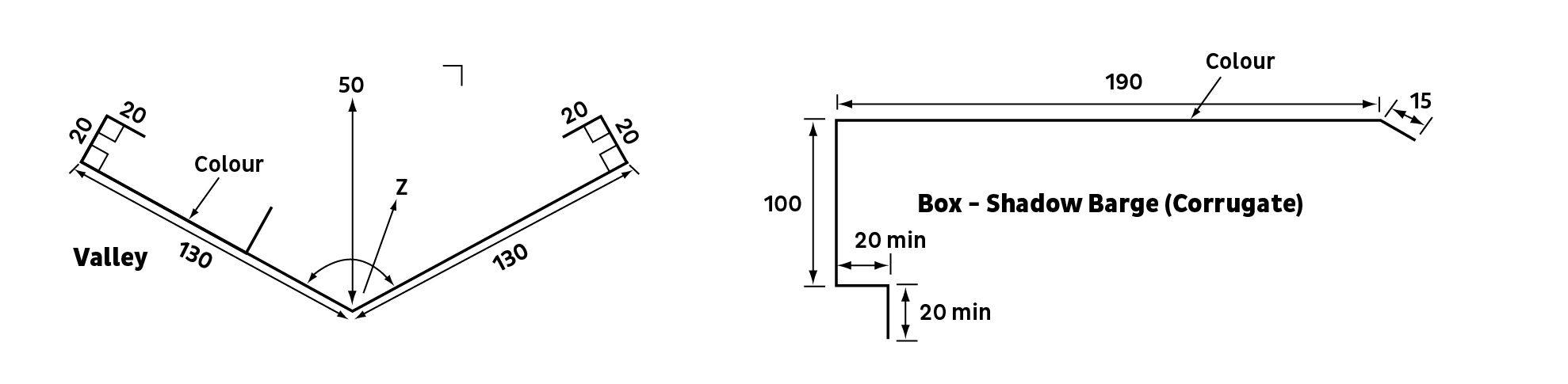
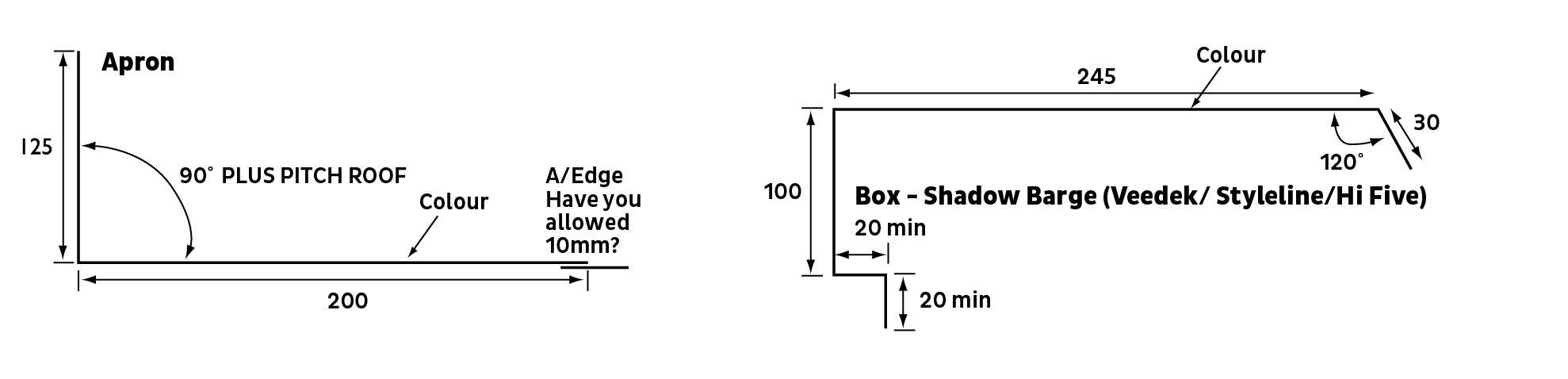
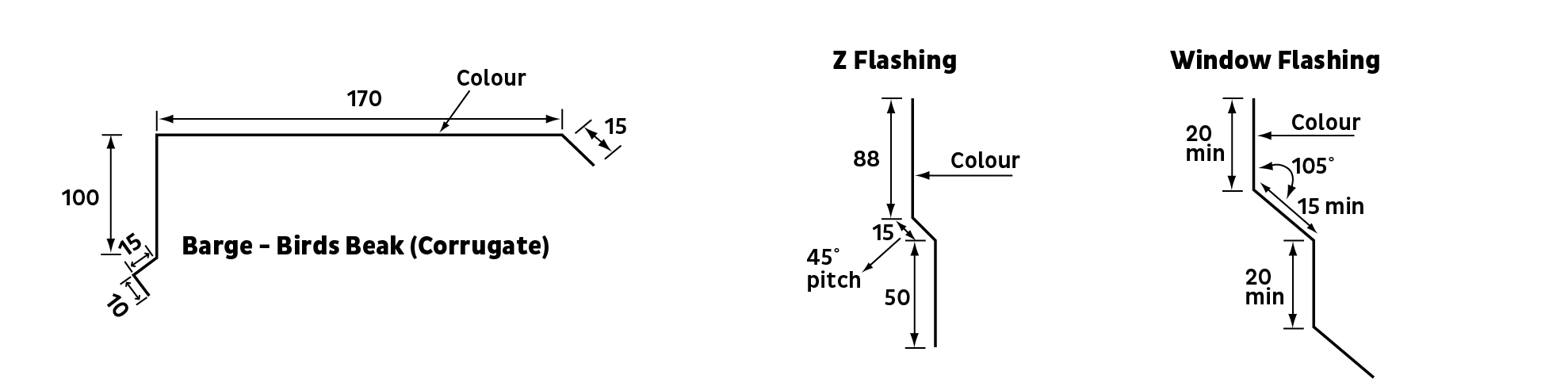
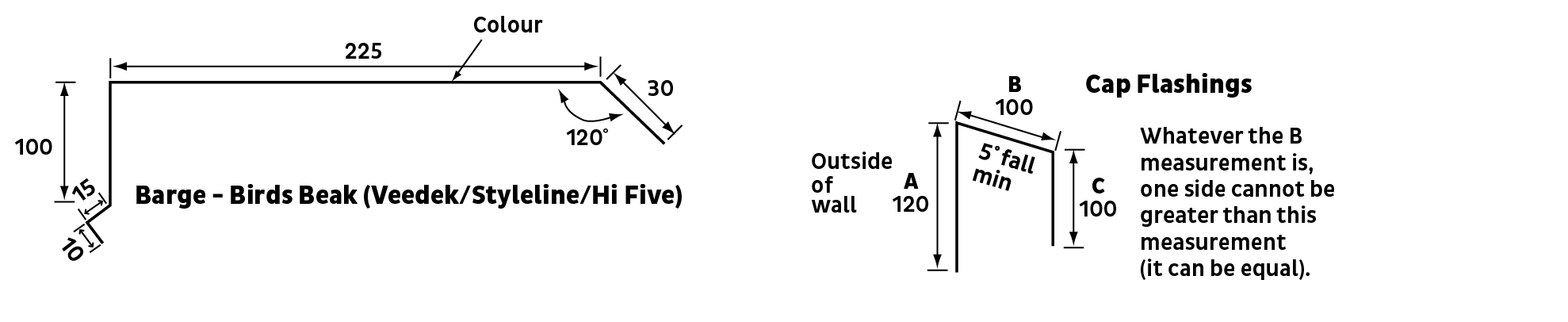
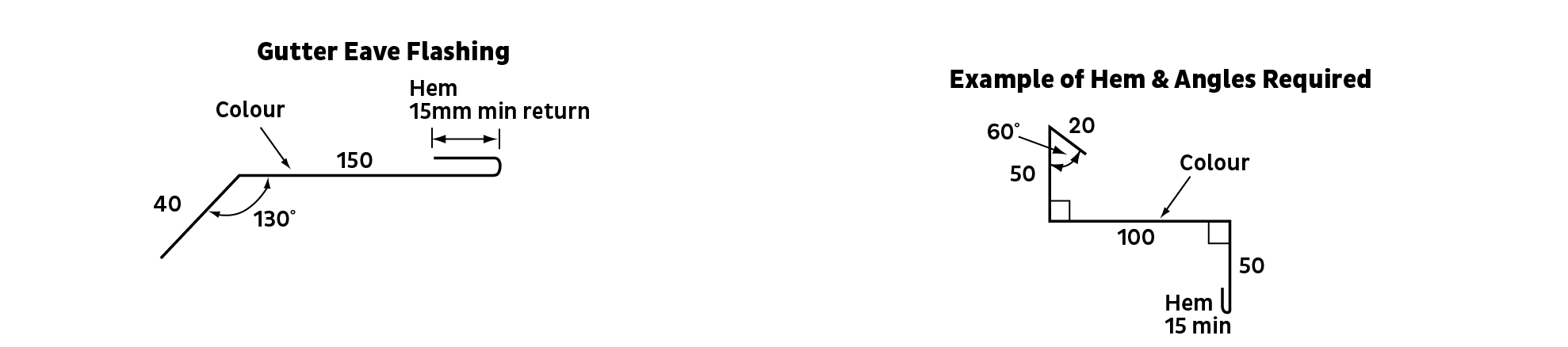
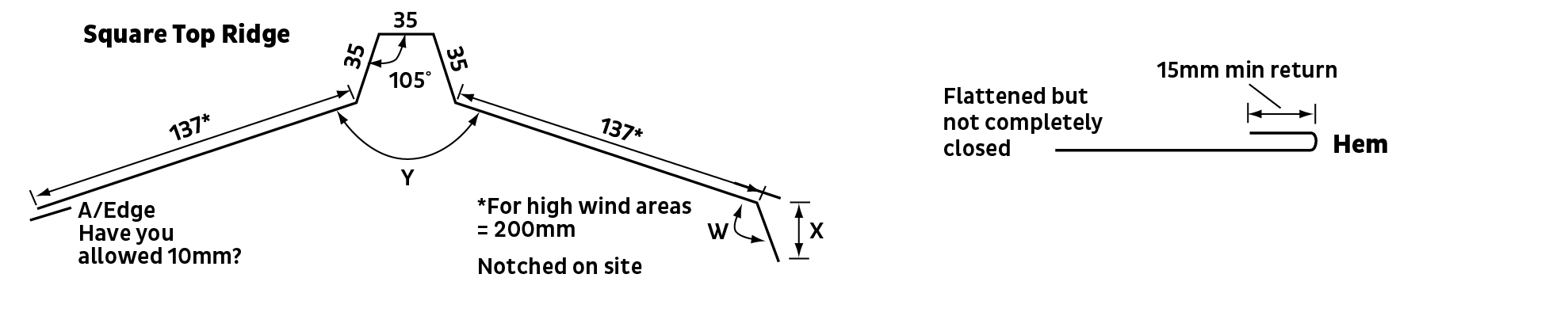
Profiled Foam Strip - Ecofoam
Product Description
Ecofoam is a polyethylene closed cell foam produced by Tetral Industries Ltd (Christchurch) for use in providing long life seals against water, draughts and pests, and is commonly used between the underside of flashings and roof or wall sheet profiles.
Features
- High tensile and tear strength.
- Resistant to most chemicals and biologically and physically inert.
- Resists embrittlement due to UV exposure.
- Profiled to fit under all the Dimond roofing profiles.
- 20mm wide with dovetailed interlocking ends.
Compatibility
Ecofoam is suitable for use with any metal roofing or cladding materials and with translucent sheeting. The carbon black contained in Ecofoam is less than 0.065% by weight and it is therefore suitable for use with Zincalume, Colorsteel and ColorCote products. Block foam – 30 x 30mm polyethylene closed cell foam. Usually ordered in for specific jobs. Allow a 14 working day lead time, for date of order to supply.
Dektite Flashings
Product Description
Dektite Flashings are a range of EPDM or silicone polymer flashings distributed in NZ by DLM, and manufactured by Deks Industries Pty Ltd (Australia). The range delivers a wide choice of specifically designed innovative products to prevent the ingress of water and dust at service pipes, flues and ducts that penetrate roofs or walls.
Dektite EPDM and silicone is compatible with Zincalume, galvanised steel, aluminium, copper, lead, asbestos cement, and even timber. Self seals at the top of the cone.
Dektite sizes are available to accommodate pipe/flue diameters from 1.0mm to 610mm.
Dektite has a wide range of configurations and sizes to suit virtually any penetration or flashing requirement.
Dektite Standard Pipe Flashing, suits flue diameters up to 450mm on Corrugate 20º roof pitch
Dektite Retrofit Flashing, suits flues up to 250mm diameter for 15º roof pitch
Dektite Soaker Flashing, suits flues up to 610mm diameter for 25º roof pitch
Dektite Retrofit Soaker Flashing, suits flues 250 to 410mm diameter
Mini Dektite Flashing, suits smaller diameter from wiring to hot water overflow pipes
Dektite Tile Flashing, suits pipe sizes up to 320mm diameter
Dektite Strip & Bullnose Flashing, 225mm wide flat strip.
Features
- Quick installation using only mechanical fasteners and sealant.
- Flexible base adapts easily to roofing shape.
- Flexible seal to pipe/flue accommodates vibration and isolates noise.
- Durable polymer material withstands UV exposure and heat.
- EPDM withstands temperatures from -30ºC to 115ºC constant and up to 150ºC intermittently.
- Silicone withstands temperatures from -60ºC to 200ºC constant and up to 250ºC intermittently.
Maintenance
No maintenance is required. In an environment that contains either chemical fumes or salt water, periodic wash down and soapy water is good practice.
Warranty
Deks Industries warrants that all Dektite flashings will perform in accordance with their published specifications, and will be free from defects in material and workmanship for a maximum period of 20 years, commencing from the date of delivery to the end user.
Flashing Design
When considering the flashings for your job be aware that our range of standard flashings are a small sample of what is possible. Below is a summary of the issues and the limitations that should be considered when detailing specific flashing shapes.
The material used will be:
Thickness
Grade
Steel
0.55mm
G300
Aluminium
0.9mm
5052/5251 - H34
Copper and stainless steel are available upon request. Please contact Dimond on 0800 DIMOND (0800 346 663) to check availability.
The girth of the flashing will be limited in one direction to 1219mm maximum (coil width). Where one dimension is 1219mm or less, the recommended maximum length (the other dimension) is 6m. Lengths longer than 6m should be avoided, as thermal expansion issues will be accentuated with flashings.
Where flashing shapes are complex or bulky, it is recommended the maximum lengths be kept to 3m to assist with handling and installation of the product. As the flashing shapes are created by mechanical folding there are certain limitations relating to the angle of the folds and the distance between two folds that need to be considered. The tightness that the material can be folded back on itself will also limit the options. The limitations will vary depending on material type including whether the material is painted. To confirm that your specific detail can be manufactured, please consult with Dimond on 0800 DIMOND during the planning stage.
Flashings running across sheet profiles must be finished to minimise the gap created over profile pans or troughs. This is achieved by notching the front downturn of the flashing over the sheet profile ribs, or on the Corrugate Profile, a soft edge to the flashing can be used. Notching should be specified as “flashing to be notched on site”.
When Duraclad is the selected roof or wall material, aluminium flashings are normally recommended. In some chemical environments, a check on the suitability of aluminium should be made.
Other things to consider in the design and installation of flashings:
- flashings must shed moisture to the outside of the building;
- flashings must not retain moisture (all flashing surfaces must maintain a minimum 3º fall);
- all flashing surfaces to be no wider than 300mm in one plane unless strengthening ribs are incorporated or there is additional support underneath;
- the cover provided shall be sufficient to ensure wind driven moisture does not enter the building. Flashings may be used either with or without compressible foam strip. When installed correctly the foam strip will restrict air flow and carriage of water under the flashing.
- where several 6m lengths of flashings are lapped end to end and joined by rivets and sealant, consideration must be given to accommodating thermal expansion if the assembled length exceeds 18m for steel or 12m for aluminium.
- details showing flashing placement for steps in long runs of roofing are shown in the detail drawings for each profile.
Change of Pitch
Where there is a change of pitch in the roof, there are two options to create a watertight junction between the roofs.
- A – include an apron flashing.
- B – run the upper roof over the lower roof.
Option A is recommended and relies on flashing cover widths as shown in the below table. This option must be used where the profile of the upper roof is different to the lower roof.
Option B while aesthetically more appealing relies on care being taken to align upper and lower sheets. However, there are certain limits which must be understood. This option is only suitable where the change in pitch is less than 20º and the lower roof can extend up under the upper roof by at least 150mm. Care will be required to avoid contact between the upper and lower sheet to ensure scratching does not occur. Movement of the top sheet through thermal expansion will also need to be considered. Maintenance is critical to remove any build-up of debris between the sheets and avoid unseen corrosion.
Whichever option is chosen, the top end of the lower sheet must be stop ended.
Fixings
As the flashings are usually located at the perimeter of the structure, they are often subjected to the highest wind pressures. Accordingly, the fixing patterns used must adequately accommodate the expected wind loads. Where a flashing covers the roof or wall cladding, the primary fastening must penetrate through to the support structure (purlin or girt). The location of the fasteners used to secure the roof will be suitable to fasten the flashing.
Where thermal expansion is being accommodated at the ridge, primary fastenings should not be used to hold the flashing. Other options such as clips will be required. Where the flashing covers a barge or parapet in low and medium wind zones, the fastener should be spaced at no more than 1m centres along the vertical face. In high wind zones and above (over 45m/sec), the maximum spacing should not exceed 500mm.
Where secondary fastenings (a fixing that secures the flashing to roof sheet only) are used to fasten the laps and provide additional hold down (side lap stitching), stitching screws are recommended. If aluminium rivets are used, the minimum diameter shall be 4.8mm.
Penetrations
When designing penetrations it is critical to understand the issues that exist when a hole is cut in the roof sheeting. Where holes exceed 200mm in either direction the structure will need to be strengthened to ensure structural integrity is maintained and fixing points for the flashing are provided. Consideration must also be given to the additional weight that may be applied to the roof structure through the placement of plant (air conditioning units) on the roof.
It is also necessary to consider the effect the penetration will have on the flow of water down the roof. In instances where large penetrations are installed, the water from several pans may be channeled into one pan beside the penetration. If the flow capacity of the pan is exceeded, flooding of the side lap may occur, or water may dam back up the sheet and flood over the back flashing positioned above the penetration.
Please consider the potential catchment area and subsequent flow rate and where necessary direct water across several pans to ensure water flow does not create a leakage issue.
Dimension excludes any soft edge or turn down to roofing.
Wall cladding must finish within 25mm above any apron flashing to allow clearance and avoid dirt building up. In high wind areas a profiled foam seal can be used under the ridge or apron flashing, over the roofing, to create a pressure differential chamber to avoid moisture being driven in. The foam seal should be placed adjacent to the stop end at the head of the sheet.
All roof and wall cladding profiles are to be stop ended at the top end of the sheet on all pitches. The cover dimensions given above are the cover over the roof or wall cladding not the leg length of the flashing.
On profiles other than Corrugate where cover over 2 ribs is required, flashings must cover at least one rib plus the trimmed side of the sheet turned up to the full height of the rib.
Flashings and Penetrations
The following comments are made as guidelines to be used when inspecting Dimond roofing and wall cladding systems during and after installation.
Material
Must be the same material and coating as the roof or wall cladding to give a similar durability and compatibility to the roof/wall system.
Fabrication
Flashings should be fabricated to achieve sufficient cover width and to maintain falls to avoid water ponding. They must be without noticeable micro-cracking and be fixed without damage such as dings or crushing, and should be free of scratches and swarf the same as for roofing.
Flashing joins must be sealed at both ends of the lap, and the fasteners must pass through the sealant at the leading edge. Spacing of fasteners should be no greater than 50mm apart. Laps to be 150mm min.
Fastening
Wherever possible, flashings should be screw fixed through to the supporting structure, with sufficient slope or fall to ensure ponding does not occur. Stitch screws should be the preferred means of attaching flashings to sheeting ribs. If aluminium rivets are used, the minimum size should be 4.8mm diameter.
All fasteners should be of sufficient size and frequency to withstand the loads that may be applied through wind uplift or thermal expansion, throughout the life of the roofing material. As a guide, where flashings cover the roof, use the same fastener that has been used to fasten the roof.
Fastener Frequency
As a guide, the fastener frequency for fixing flashings should be:
Wind Zone* | Fasteners Per Metre |
Low (32 m/s) | 1 |
Medium (37 m/s) | 2 |
High (44 m/s) | 3 |
Severe (50 m/s) | 4 |
* in accordance with NZS 3604
Sensible allowance should be made to allow relative thermal expansion between flashings and sheeting if sheet lengths exceed 12m. Expansion joints in the flashings should be considered for steel flashings greater than 18m and aluminium flashings greater than 12m in length.
Flashing lapping over roofing should be in accordance with Table 2.1.O of Section 2.1.3.6 of the Dimond Roofing & Cladding Technical Manual. Where barges meet the gutter, this must be closed off to ensure wind driven moisture and birds cannot enter the building.
Profiled Foam
Profiled foam sealing strips should be installed when specified at the top end of the sheet, adjacent to the stop end. To help keep the strips in place it is good practice to position them on a bead of silicone sealant.
Notching
Best practice to notch flashing downturns around sheet profiles is to mark in-situ and use a rib-shaped template. Clearance gaps around the ribs should be just sufficient to prevent cut edge contact with the sheet surface. Gaps between 1mm and 3mm are generally considered satisfactory.
Soft edging can be used on corrugate and low rib profiles with rib heights up to 30mm and should be neatly pushed down and formed in to the profile pans to achieve a neat-tight fit.
Property boot pipe flashing
Property boot pipe flashings must not be positioned in such a way that a dam is formed across a water channel. It is preferred that Property boot pipe flashings are positioned on the 'bias' rather than square across the sheet. If the pipe and Property boot pipe flashing dam up the pan or restrict more than 50% of the water flow around the pipe and flashing, an additional cover over flashing to the ridge and sealing of the Property boot pipe flashing to this flashing should be considered. Excess silicone sealant should be avoided, as it will add to he risk of water ponding.
Penetrations
Penetration holes with their major dimension or diameter greater than 150mm must have support framing placed around the perimeter of the penetration holes.
Water diversion around the penetration must not cause an overload of the receiving channel such as the pans that the water has been diverted into, which may cause flooding. Penetration flashing shall not rely solely on the silicone sealant to achieve weather tightness of the flashing.